Israel is a small state with a single coastline, and 7 mega-size desalination plants built or planned along this strip of coast, for a length of approximately 200 km, currently producing some 80% of.
Pressure Center Design: Powering Desalination Efficiency and Sustainability
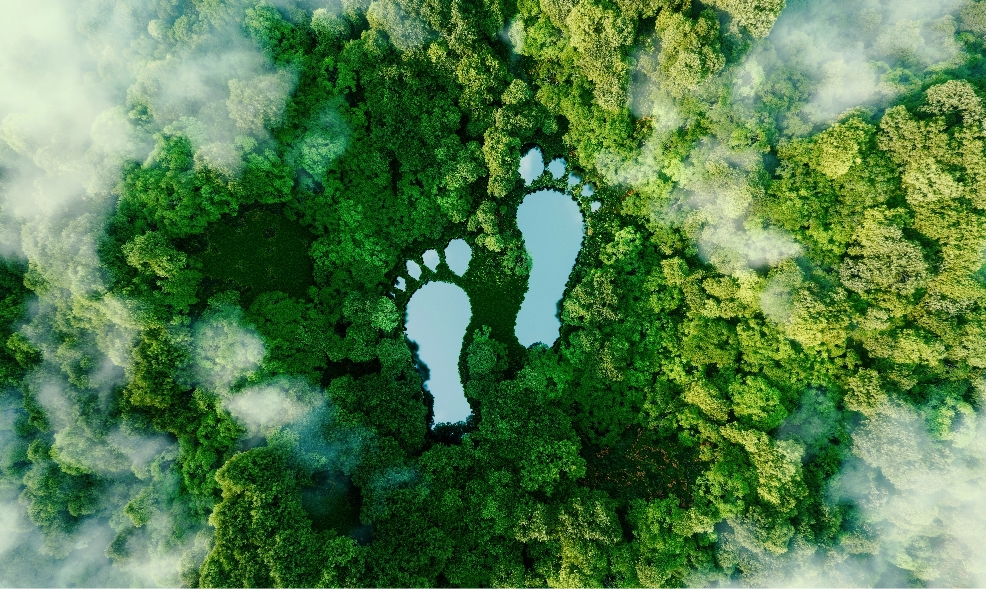
Desalination technology has become an essential solution for providing fresh water to serve the continuously growing population and ensure water security. As climate change becomes more of an issue, the demand for desalination technology has increased rapidly.
In Israel, located in the heart of the water-scarce Middle East, ingenuity and innovation for overcoming the challenges posed by limited freshwater resources have been present from the country’s birth. With over 80% of the country’s domestic water consumption relying on desalination, Israel has emerged as a pioneer in innovative water solutions.
IDE has been a significant player in the desalination industry for over 60 years, developing several innovative technologies to enhance the performance, efficiency, and reliability of desalination plants. One such innovation that has allowed us to set a new benchmark for the low cost of desalinated water is the Proprietary Pressure Center Design. It has been implemented in several plants and has operated successfully for almost two decades.
Pressure Center Design, a Paradigm Shift in Desalination
Traditional desalination plants have typically relied on individual train configurations for Reverse Osmosis (RO) processes. With the appearance of large desalination projects, IDE developed a new design approach; Pressure Center. Pressure Centre systems reduce the cost of water. The Pressure Center Design challenges the conventional approach to desalinating water. It includes three main components:
Pumping Center: Large (High Pressure) HP pumps which feed all the RO trains.
RO Membrane Trains: Pressure vessels which contain eight RO elements.
Energy Recovery System (ERS): One common block of ER devices which serves all RO trains.
This proprietary design reduces energy consumption by using large HP pumps that operate at a higher rate of efficiency. The equipment arrangement in the Pressure Center allows the disconnection of the HP pump from the RO trains and allocates them to common pressure centers. The pumping center is composed of a number of large high-pressure (HP) pumps, 5 – 7 MW each. Instead of an individual RO train configuration, the Pressure Centre consolidates key components into a single mega-modular RO system and brings together high-pressure pumps, energy recovery systems, and RO membranes into a unified, interconnected design. The outcome? This design reduces energy consumption and increases the system’s availability and reliability. But there are more advantages…
The Multifaceted Advantages of the Pressure Center Design
The Pressure Center Design optimizes space utilization, reducing the physical footprint of desalination plants. This space efficiency translates into lower capital investment and construction costs. The design’s interconnectedness enhances operational flexibility and provides better equipment redundancy and availability. Pressure Centre Design allows the plant to operate at different production rates without sacrificing overall plant performance. The concept’s adaptability contributes to increased plant reliability.
Energy consumption in desalination processes often constitutes a significant environmental concern. The Pressure Centre’s energy efficiency directly contributes to reducing carbon footprints. Integrating green energy sources, such as solar power and an innovative steam-direct solution patented by IDE, is mainly supported by the Pressure Center design, which helps to further minimize the environmental impact. This approach aligns with global efforts to transition towards renewable energy and reduce greenhouse gas emissions. The design’s energy efficiency aligns with sustainability goals by minimizing energy consumption.
IDE Pressure Center Concept
Pressure Center Design Drives Operational Efficiency
Two of IDE’s highly decorated desalination plants serve as prime examples of the effectiveness of Pressure Centre Design: Hadera in Israel and Carlsbad in California, USA.
The Hadera Desalination Plant, capable of producing over 137 million gallons of potable water daily, showcases the benefits of the Pressure Center’s operational flexibility. The Pressure Center Design’s innovative operation modes amplify its efficiency gains. In the Hadera plant, these modes enabled the development of production regimes that were strategically designed to align with variable electricity tariffs. By varying production rates during peak and off-peak hours, the plant was able to optimize energy consumption. This dynamic operation not only reduces energy costs but also showcases how advanced technology can align with economic objectives.
The Carlsbad Desalination Plant, the largest in the Western Hemisphere, highlights the design’s ability to maintain steady membrane performance while dealing with severe algae bloom events which can disrupt the plant’s operation and hinder production. However, the Pressure Center Design’s operational flexibility offers a solution. During times of algae bloom or maintenance requirements, the design enables plant operators to adjust production rates without compromising water quality or quantity. This adaptability is essential for meeting water demands under diverse circumstances.
When Financial Efficiency and Sustainability Go Hand in Hand
In the quest for sustainable water solutions, the Pressure Center Design represents a transformative step forward. Through its space efficiency, operational flexibility, and environmental benefits, this design approach addresses both water scarcity, cost of water, and environmental concerns. As we continue to grapple with growing water demands and climate change, the Pressure Center Design exemplifies the potential of innovation to solve these pressing global challenges with a solution that is cost-effective, reliable, and sustainable.