In today’s era of growing industrial demands and environmental challenges, water management has become a crucial aspect of sustainable development. Efficient water.
Why Water Sustainability is Vital for the Semiconductor Industry
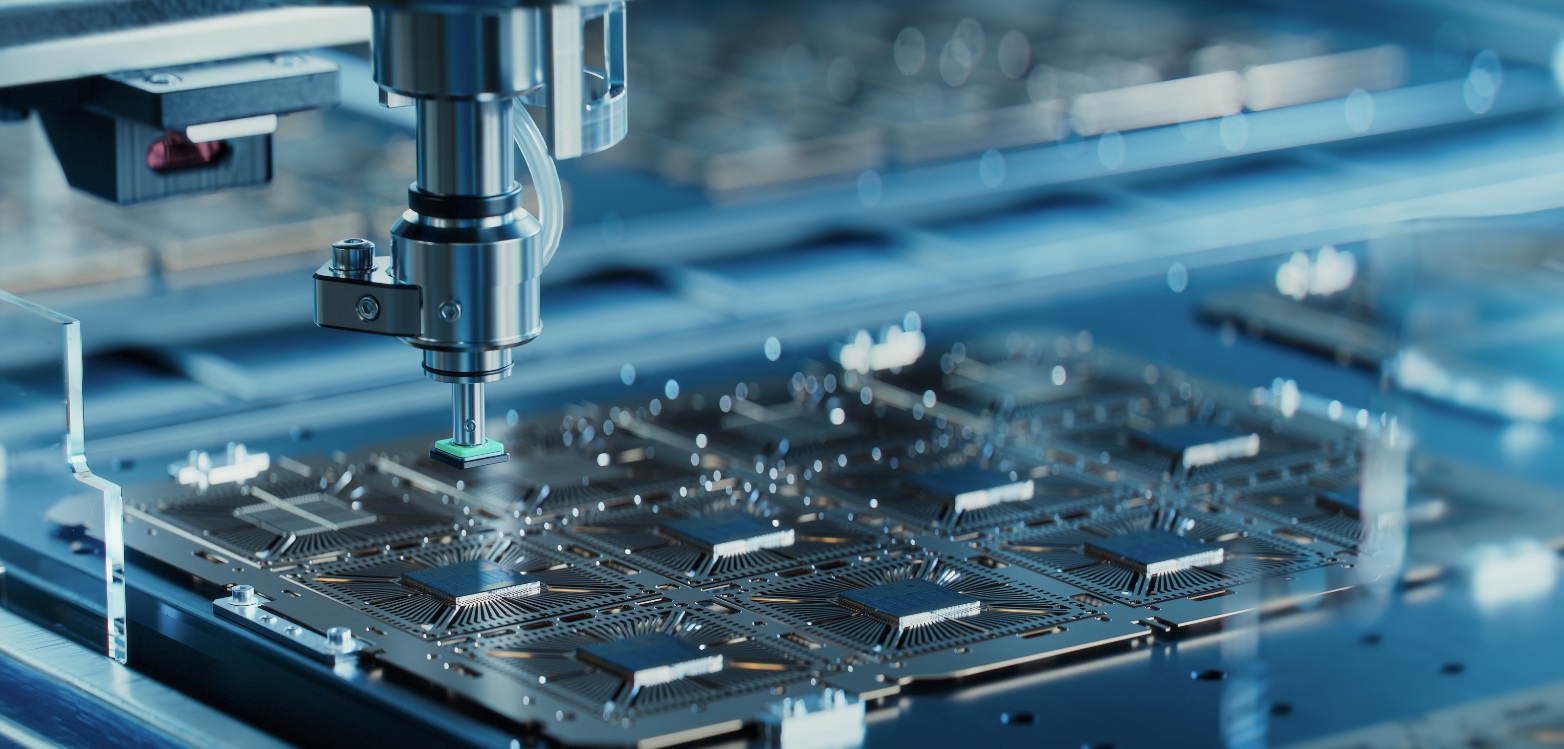
In semiconductor manufacturing, the fabrication process of silicon semiconductor devices usually consists of six universal steps: oxidation, lithography, etching, doping, chemical vapour deposition, and metallization. These stages are crucial for shaping the silicon wafers and creating the intricate circuitry that forms the basis of semiconductor devices.
Half of these manufacturing processes require ultra-pure water usage to maintain the integrity and quality of the semiconductor devices. During the oxidation step, ultra-pure water is utilized for cleaning and rinsing purposes, to ensure the purity of the oxide layer formed on the surface of silicon wafers. In the lithography stage, ultra-pure water plays a critical role in cleaning and rinsing the wafers after each exposure to remove any residual photoresist or contaminants, thereby preserving the accuracy and precision of the transferred patterns. Finally, in the chemical vapour deposition process, ultra-pure water serves as a solvent and rinsing agent to prepare precursor solutions and clean the deposition chamber, facilitating the deposition of thin films onto silicon wafers with utmost purity and reliability.
The numbers related to semiconductor manufacturing water usage are staggering:
- In semiconductor fabs, about three-quarters of the total water used is directly related to the manufacturing process.
- Generating 1,000 gallons of UPW consumes approximately 1,400 to 1,600 gallons of municipal water.
- A large semiconductor fabrication facility (Fab) processing around 40,000 wafers monthly could consume up to 4.8 million gallons of water daily. This is equivalent to the annual water consumption of a city inhabited by 60,000 people.
Challenges and Risks for Semiconductors
The rapid expansion of the semiconductor industry presents a significant challenge in terms of sustainable water management. The risks associated with unsustainable semiconductor manufacturing water usage are multifaceted and can have significant implications for both the industry and the environment.
Some of these risks include:
Environmental Impact and Sustainability: Unsustainable water usage can lead to the depletion of local water sources and ecosystems, impacting aquatic habitats, biodiversity, and water quality. Discharging untreated or inadequately treated wastewater into water bodies can also contribute to pollution, harming aquatic life and ecosystems.
Regulatory Compliance: Regulatory bodies impose strict standards and regulations on water usage and wastewater discharge (both in terms of quality and quantity) to protect water resources and public health. Non-compliance with these regulations can result in legal consequences, fines, and reputational damage for semiconductor companies, affecting their operations and bottom line.
In recent years, regulators have increasingly focused on the issue of PFAS (Per- and Polyfluoroalkyl Substances) contamination. These synthetic chemicals, used across various industries, pose significant health and environmental risks. Although the primary regulatory focus has been on drinking water, there is growing concern about PFAS presence in wastewater. In the semiconductor manufacturing sector, PFAS-containing chemicals and materials can lead to contamination as they enter wastewater streams. As awareness of this issue grows, regulatory agencies are expected to develop more stringent guidelines and standards specifically targeting PFAS in wastewater discharges.
Water Scarcity: In regions experiencing water scarcity or drought conditions, competition for water resources can intensify, leading to conflicts with local communities, agriculture, and other industries. A recent analysis of the S&P Global ratings states that “We view water scarcity as a risk in the coming decade for the tech hardware industry, particularly the water-intensive semiconductor subsector. Mishandling of such a risk could hit a chipmaker’s operations and creditworthiness.”
POTW (Publicly Owned Treatment Works) infrastructure limitations:These limitations constrain both the expansion of raw water piping into fabrication facilities and the transportation of effluent out of the facilities post-manufacturing. The inability to expand raw water piping can impact production capacity and efficiency while limitations in effluent transportation hinder proper wastewater management and environmental compliance, potentially leading to the accumulation of untreated wastewater within facilities, posing environmental risks and regulatory compliance issues.
Interruption to Production: Water shortages or interruptions in the water supply can disrupt semiconductor manufacturing operations, leading to production delays, increased costs, and reduced productivity.
Financial Costs: Unsustainable water usage practices can incur significant financial costs for semiconductor companies, including expenses related to water procurement, treatment, and disposal.
Reputation and Stakeholder Relations: Negative publicity surrounding water-related issues, such as pollution incidents or water scarcity concerns, can damage a semiconductor company’s reputation and erode stakeholder trust.
The Path to Resilience: Sustainable Water Management
Addressing these above risks requires semiconductor companies to adopt sustainable water management practices, mainly recovering as much water as possible within their processes. This is where industrial water treatment comes to play.
The conventional approach for water treatment in the semiconductor industry follows the Membrane Bio-Reactor (MBR) treatment which utilizes the pH RO process (High-Efficiency Reverse Osmosis) which is extremely efficient for water containing silica. This process, although capable of addressing some of the most challenging industrial feedwater and wastewater issues and achieving high recovery rates, demands considerable effort and extensive chemical use. Moreover, the process is highly sensitive; minor errors can damage equipment, complicating the desalination process and reducing efficiency.
Innovative Solutions for Semiconductor Water Treatment
IDE has pioneered a groundbreaking industrial water treatment technology that addresses many of the challenges inherent in traditional methods. This innovative solution combines two synergistic technologies: Pulse-Flow Reverse Osmosis (PFRO) and MAX H2O Desalter. Together, these technologies facilitate high water recovery rates, bypassing the complexities and intensive chemical requirements typical of conventional methods such as the pH RO process. Notably, PFRO and MAX H2O Desalter also significantly lower capital costs, reduce the physical footprint, and cut operational expenses.
PFRO operates uniquely as a single-stage process, discharging brine at a high rate, in periodic pulses lasting a few seconds, followed by extended periods of 100% recovery without brine discharge. These short cycles of concentration and intensive flushing, shorter than the induction time, enable PFRO to achieve extremely high supersaturation of dissolved minerals, preventing crystal formation, preventing biofouling and scaling and allowing for significantly higher recovery rates compared to conventional RO systems.
Additionally, PFRO reduces capital and operational expenses by decreasing power consumption and pressure drops through non-continuous brine pumping, along with requiring fewer pressure vessels and membranes, resulting in cost savings. The elimination of brine recycling further contributes to lower power consumption and increased system efficiency. Moreover, PFRO systems are modular and scalable, seamlessly integrating into new plants or retrofitting into existing facilities, and can function as standalone systems or in parallel with conventional RO systems
A recent IDE project with an industrial semiconductor manufacturer to design and build IDE’s Pulse Flow RO (PFRO) system for brine minimization at the customer’s facility, successfully achieved a recovery rate of 54%, increasing the overall facility recovery to 88%.
The Business Case for Water Sustainability
Adopting sustainable water management practices offers significant cost savings and efficiency improvements for semiconductor companies, known for their high water usage. By implementing more efficient water recycling systems, these companies can drastically reduce the volume of freshwater required and lower their water procurement costs. Advanced treatment technologies allow for the reuse of wastewater, reducing disposal and compliance costs. Efficient water management and semiconductor manufacturing water usage also correlates with reduced energy consumption as less energy is needed for heating, cooling, and transporting water, directly lowering operational costs.
By focusing on sustainable water management, semiconductor companies not only address the ethical aspects of resource conservation but also significantly enhance their operational efficiency and cost-effectiveness. This strategic focus ultimately contributes to a more resilient and financially stable business model.