In today’s era of growing industrial demands and environmental challenges, water management has become a crucial aspect of sustainable development. Efficient water.
Innovative Solutions in Cooling Tower Blowdown Water Treatment
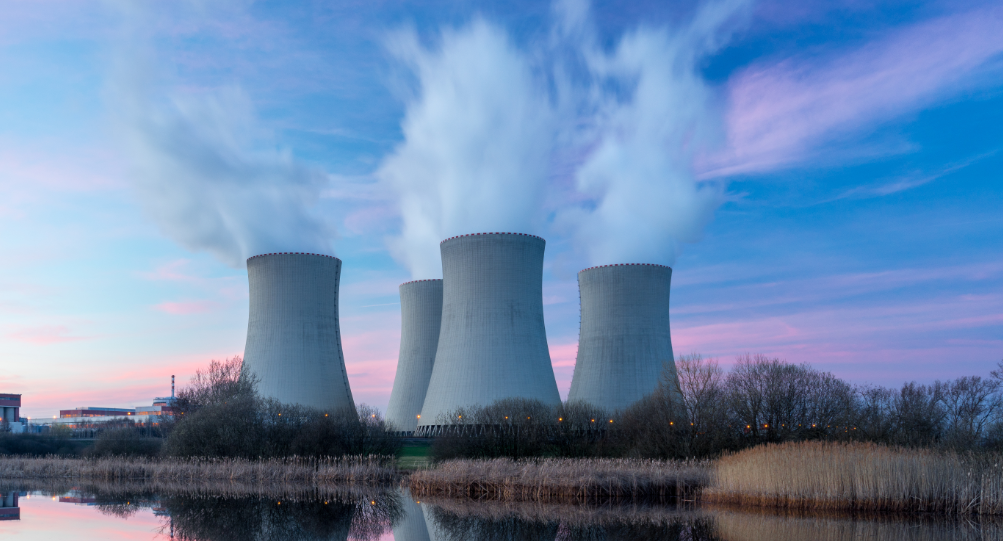
Cooling Tower Blowdown – What is it all about?
Cooling towers are widely used in many industries such as power generation, petroleum refining, chemical processing, semiconductor, and many others. These towers help remove heat generated by various plant processes through water evaporation. As the water evaporates, the minerals and impurities dissolved in it remain, becoming more concentrated. Consequently, cooling towers require to blowdown a portion of the circulated water in the tower and to treat it or dispose of this concentrated water stream.
Cooling Tower Blowdown – How do you manage it?
In some cases, where regulations permit, cooling tower blowdown can be managed through discharge to a nearby surface water source or alternatively to the local wastewater treatment plants.These are probably the most cost effective solutions. However, in most cases, strict guidelines by state regulators concerning disposal of the cooling tower blowdown to the environment do not permit it. Impurities such as sulfates, total dissolved solids (TDS), chlorides, organic content, phosphates and various other contaminants must be removed so disposal will be allowed. Due to this, other disposal methods are applied such as evaporation ponds or injection into deep wells. These solutions are expensive to build, to maintain and operate. The larger the blowdown stream is, the higher the disposal cost.
The Benefits of Effective Cooling Tower Blowdown Management
Due to the above, plants that operate cooling towers are continually looking for ways to minimize the size of the blowdown stream as much as possible and to treat the blowdown so that water can be recirculated back as make-up to the tower.
Apart from reducing the capacity of the blowdown stream and minimizing disposal costs, water scarcity is becoming increasingly critical in many regions around the world. State regulators often prioritize public users, reducing the water available for industrial purposes, which can negatively impact the operational flexibility and expansion plans of a plant. Consequently, treating the blowdown or makeup water to recover clean water becomes a crucial strategy. This cooling tower blowdown water treatment enables the recycling of the treated blowdown back into the cooling tower as high-quality makeup water. Such a process increases the cooling tower’s cycles of concentration, dramatically reducing the consumption of both blowdown and makeup water. Ultimately, this strategy not only provides additional water capacity needed for greater operational flexibility but also significantly reduces reliance on external water sources.
Moreover, increasing the cycles of concentration and recycling treated water from the blowdown stream can potentially reduce make-up water treatment chemical costs, if such are applied.
Challenges in Cooling Tower Blowdown Treatment
Cooling tower blowdown contains high concentrations of sparingly soluble salts, which present significant challenges in terms of recovery and often result in high operational expenses for most treatment technologies. One of the primary challenges in membrane technologies is the formation of deposits such as gypsum, calcium carbonate, and silica on the membranes. These deposits can severely impede the efficiency and effectiveness of the treatment process.
Additionally, fouling and biofouling is a major concern in the treatment of cooling tower blowdown. This is especially problematic for membrane-based technologies, as the relatively high organic content in the water and the biological growth can dramatically reduce the performance and longevity of the membranes. Managing fouling and biofouling is crucial to maintaining optimal functionality and preventing costly downtime or maintenance.
Existing Technologies – Why are they not good enough?
Existing solutions designed to address these water treatment challenges, including reverse osmosis (RO) or multi-stage RO often struggle to meet the desired performance. Typically, these technologies offer low recovery rates, around 50 to 60% in a single-stage configuration, and are vulnerable to issues like excess gypsum, silica deposition, and biofouling. In addition, 50%-60% recovery is usually too little and still bears significant disposal cost for the plant and therefore plants are looking for higher recovery solutions. Those that do achieve high recovery standards, apply reverse osmosis solutions coupled with various types of treatments such as chemical precipitation, softening, electrocoagulation, EDR and various other treatment combinations. However, these approaches do so at a high capital and operational cost
Moreover, many of these systems fail to maintain consistent performance when the quality of the blowdown varies, and quite often generate a considerable amount of sludge, compounding disposal and handling issues.
IDE’s MAX H2O Desalter – A cost effective high recovery sustainable solution
IDE developed a membrane-based technology, The MAXH2O Desalter, that maximizes high recovery of CTBD and reuses most of the treated water as makeup. The technology contains a single stage reverse osmosis system, with an integrated salt precipitation unit. This technology operates by recirculating the CTBD through the RO system, followed by a fluidized bed reactor in which controlled precipitation of supersaturated sparingly soluble salts is performed.
This cyclic process, which occurs in small and controlled intervals, allows for a continuous concentration and precipitation of the salts that would otherwise limit the recovery, and does so without increasing the scaling and biofouling inside the membranes, thus enabling extremely high recovery (rates beyond 95%). The produced by-products contain over 90% solids, which lead to easy and cost-effective disposal without additional sludge minimization processes.
The MAX H2O Desalter can be integrated either as a standalone downstream solution for cooling tower blowdown treatment, or as an upstream solution for full zero liquid discharge treatment to eliminate any liquid discharge out of the plant. The MAX H2O Desalter produces high quality permeate for process reuse or makeup to the towers, to comply with the discharge regulation, or to minimize the downstream ZLD thermal units.
Learn more about IDE’s Desalter solutions for maximizing cooling tower blowdown management in this webinar.
Demonstrating Success in Real-World Applications
In a recent case study conducted at a power plant in Chile, a demonstration unit operated continuously for 60 days, achieving an impressive 93.5% water recovery. This demonstration of the IDE process showcased its robustness and reliability for Cooling Tower Blowdown (CTBD) treatment.
Typically, with conventional technologies, membrane scaling limits recovery to only about 50%. However, using the MAX H2O Desalter, we achieved a significantly higher recovery rate. This advancement presents a viable solution that can substantially reduce operational costs and enhance efficiency in managing CTBD not only in power plants but across various industries.
Learn how MAX H2O helps minimize water usage in power plants.
The Bottom Line?
In a world increasingly grappling with water scarcity, effective blowdown management in cooling tower systems represents a crucial advancement for industrial plants. By optimizing water recovery to achieve high-quality standards, often surpassing the quality of the original makeup water, these systems significantly reduce the need to draw from external water sources. This not only conserves precious resources but also drastically cuts the costs associated with disposing of waste.
In environments where regulations are stringent or where plants are committed to enhancing their sustainability practices, employing MAX H2O allows for maximizing blowdown efficiency, driving sustainability, reducing costs, and protecting our planet’s vital water resources.
Learn how IDE’s cooling tower blowdown water treatment technology can help your plant maximize recovery, minimize operational costs and comply with the strictest regulatory requirements.
Contact our Experts.