In today’s era of growing industrial demands and environmental challenges, water management has become a crucial aspect of sustainable development. Efficient water.
Overcoming PFAS Challenges in Semiconductor Manufacturing
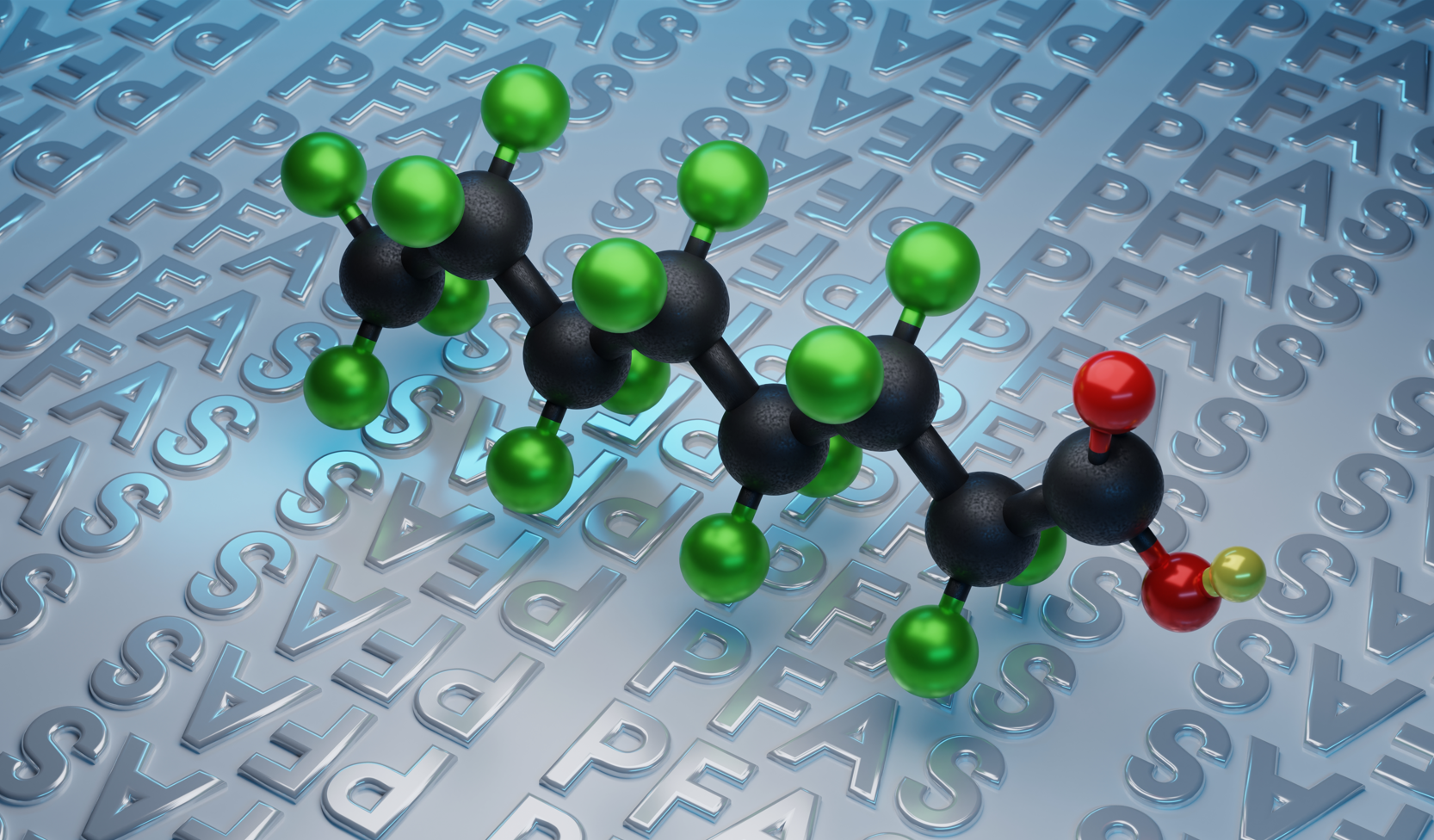
The increasing regulation of per and polyfluoroalkyl substances (PFAS) is becoming a pivotal issue for industries worldwide. For semiconductor manufacturers, a sector heavily reliant on PFAS for essential production processes, navigating these regulations requires innovative solutions and a forward-thinking approach.
What Are PFAS and Why Are They a Problem?
Per- and polyfluoroalkyl substances (PFAS) are a class of approximately 15,000 synthetic chemicals commonly used to make products resistant to heat, water, grease, and stains. Found in a wide range of industrial and consumer applications, PFAS are valued for their durability and unique chemical properties.
However, this durability comes at a cost. Often called “forever chemicals,” PFAS do not naturally break down in the environment, leading to widespread contamination of water, soil, and air. Even at trace levels, PFAS have been linked to severe health issues, including cancer, thyroid dysfunction, liver damage, decreased immunity, and developmental problems. Their persistence and mobility mean they can travel long distances, accumulate in living organisms, and pose long-term risks to ecosystems and human health.
Addressing PFAS contamination is a pressing global challenge, requiring innovative solutions to mitigate their impact and protect environmental and public health.
Understanding PFAS and Their Role in Semiconductor Manufacturing
In the semiconductor industry, PFAS are indispensable. They are used in up to 1,000 nanometric-level processes, such as photolithography and plasma processing, making them critical to chip production. However, the same properties that make PFAS valuable in manufacturing; resistance to degradation and stability, also make them challenging to manage and remove from wastewater.
The Regulatory Landscape for PFAS
Global awareness of PFAS contamination has driven stricter regulations worldwide. In the United States, the Environmental Protection Agency (EPA) has set stringent limits for PFOS and PFOA in drinking water, with legal thresholds as low as 4 parts per trillion (ppt). By 2027, water systems must begin testing for six PFAS compounds, report results in annual Water Quality Reports, and notify customers of any violations. Systems must comply with these thresholds by 2029, either through advanced treatment solutions or alternative PFAS-free water sources.
These municipal regulations mark a crucial step in addressing PFAS contamination, but they also pave the way for broader accountability under the Comprehensive Environmental Response, Compensation, and Liability Act (CERCLA). In 2023, the EPA proposed designating PFOA and PFOS as hazardous substances under CERCLA, empowering the agency to enforce cleanups, recover costs from responsible parties, and hold polluters accountable. Facilities releasing over one pound of PFAS within a 24-hour period would be required to report these discharges, significantly enhancing oversight and mitigation efforts. For industries involved in PFAS production, use, or disposal, this designation presents substantial legal and financial risks.
For the semiconductor industry, which generates PFAS-laden wastewater, this poses a unique challenge. Testing data from a U.S. semiconductor plant in 2022 revealed PFAS concentrations as high as 78,000 ppt in wastewater streams, vastly exceeding regulatory limits.
Tackling PFAS in Semiconductor Production
Addressing PFAS in semiconductor manufacturing presents unique challenges due to the pervasive use of these chemicals in critical production processes. There are several pathways manufacturers can consider to tackle PFAS contamination effectively:
1. Eliminating PFAS Usage
While phasing out PFAS entirely may seem like an ideal solution, it is impractical for semiconductor manufacturing at this stage. PFAS are deeply embedded in critical processes, and no readily available substitutes offer the same performance and reliability. Completely removing PFAS would require years of research and development, significant investment, and potentially disruptive production overhauls.
2. Targeted Treatment of Specific Streams
Another approach is to isolate and treat specific streams containing high PFAS concentrations. This involves identifying and separating PFAS-laden streams from the broader wastewater output. However, this method is often prohibitively expensive and operationally complex. Semiconductor production processes have been built and optimized over decades, making the segregation of streams a challenging task that could interfere with established workflows.
3. Treating the Outfall Stream for Reuse
The most feasible and sustainable option for semiconductor manufacturers is to focus on treating the outfall stream, where PFAS accumulates for reuse. By treating wastewater at this stage, manufacturers can address PFAS contamination without disrupting existing processes. This approach also aligns with broader sustainability initiatives, such as achieving water-positive goals, advancing ESG commitments, and reducing environmental impact.
Challenges with Short-Chain PFAS
Once the decision has been made to treat PFAS in the outfall stream, we need to choose the best treatment method. PFAS management in semiconductor facilities presents unique challenges due to the varying chain lengths of these compounds. Long-chain PFAS are relatively easier to capture and treat, but short-chain PFAS, such as C3 and C4 variants, are highly mobile, resistant to traditional treatment methods, and more difficult to remove effectively.
There are three main approaches to managing PFAS in semiconductor manufacturing:
1. Carbon Adsorption (GAC)
Granular activated carbon (GAC) is a widely used technology for PFAS removal. It works well for longer-chain PFAS compounds but struggles with short-chain variants such as C3 and C4 compounds, which are increasingly prevalent in semiconductor manufacturing.
2. Ion Exchange Resins
Ion exchange resins can be effective in removing specific PFAS compounds. However, their efficiency decreases for ultra-short-chain PFAS and when treating complex wastewater matrices.
3. Reverse Osmosis (RO) or Nanofiltration
Reverse Osmosis (RO) and nanofiltration (NF) are highly effective for removing both long and short-chain PFAS. These membrane technologies can capture a broad spectrum of PFAS, making them ideal for treating wastewater in semiconductor facilities. RO and nanofiltration are also effective at achieving high recovery rates, supporting broader water recycling initiatives.
The Case for Zero Liquid Discharge (ZLD)
While RO and NF excel at isolating PFAS from the wastewater stream, they generate a concentrated brine that still requires careful management.
This is where Zero Liquid Discharge (ZLD) becomes a natural extension of the RO process. By incorporating ZLD, the concentrated PFAS brine from RO can be further treated, reducing it to solid waste. This approach not only ensures the safe disposal of PFAS but also minimizes water waste by enabling complete recovery and reuse of treated water.
ZLD systems complement RO by closing the loop on PFAS mitigation, aligning with semiconductor manufacturers’ water-positive goals and broader ESG commitments. Together, these technologies create a robust and sustainable solution for managing PFAS in an environmentally responsible manner.
What about Full PFAS Destruction?
While current technologies focus on removing PFAS from wastewater, the ultimate goal is full PFAS destruction. Emerging techniques are being explored to break down PFAS into harmless components, but these solutions are still in the developmental stage. In the meantime, combining effective removal technologies with robust waste management practices is the best course of action.
Semiconductor Manufacturers Must Take the Lead
PFAS are a critical issue for semiconductor manufacturers, both from an operational and regulatory perspective. With the right wastewater treatment strategies, companies can address these challenges while advancing their sustainability goals.
At IDE, we specialize in PFAS removal solutions tailored for semiconductor manufacturers. Our advanced RO and Nanofiltration technologies, powered by 60 years of experience and over 400 water treatment projects across the globe ensure compliance with stringent regulations and support a cleaner, more sustainable future.
Ready to tackle PFAS in your semiconductor operations?
Schedule a demo with IDE experts today and discover how we can help you achieve your goals.